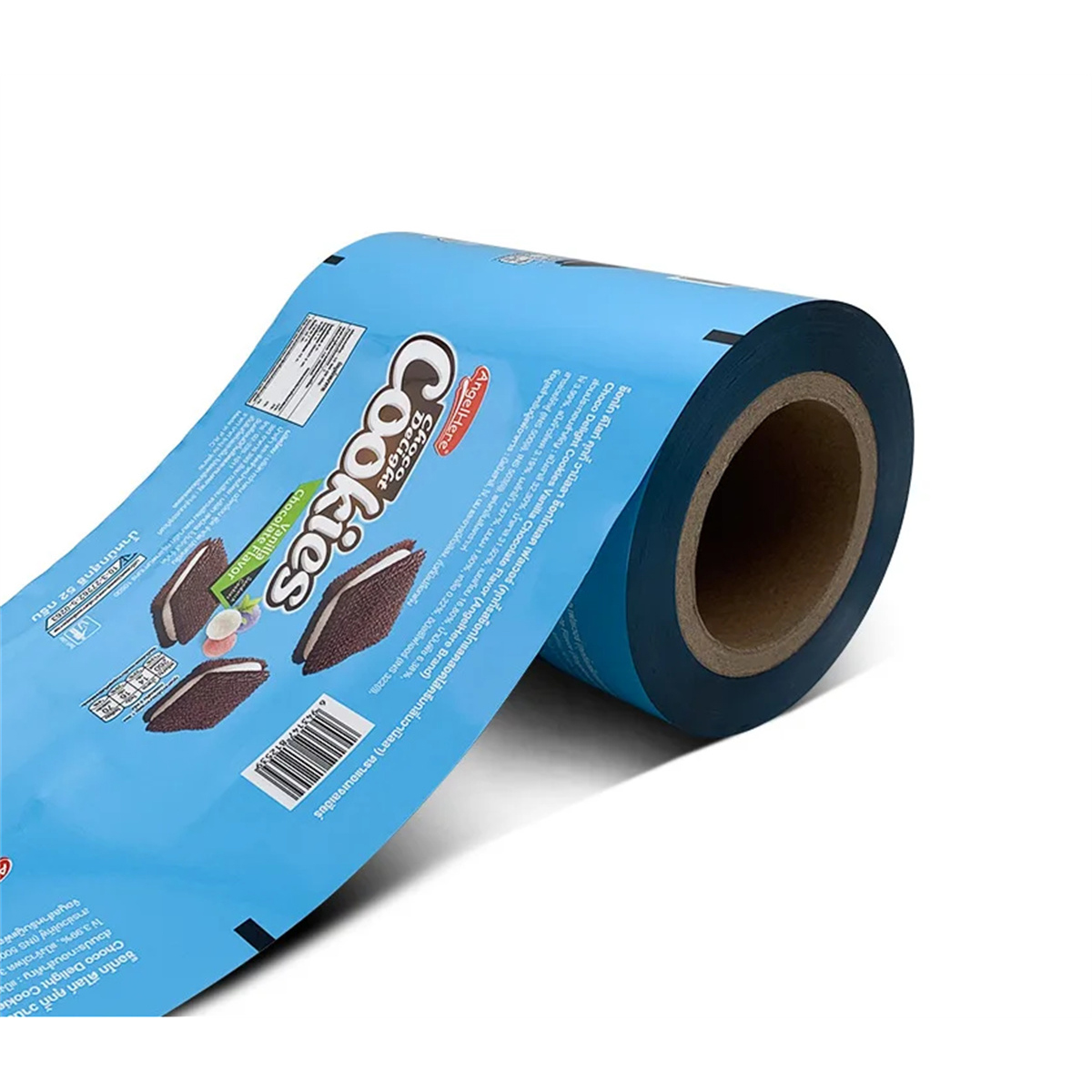
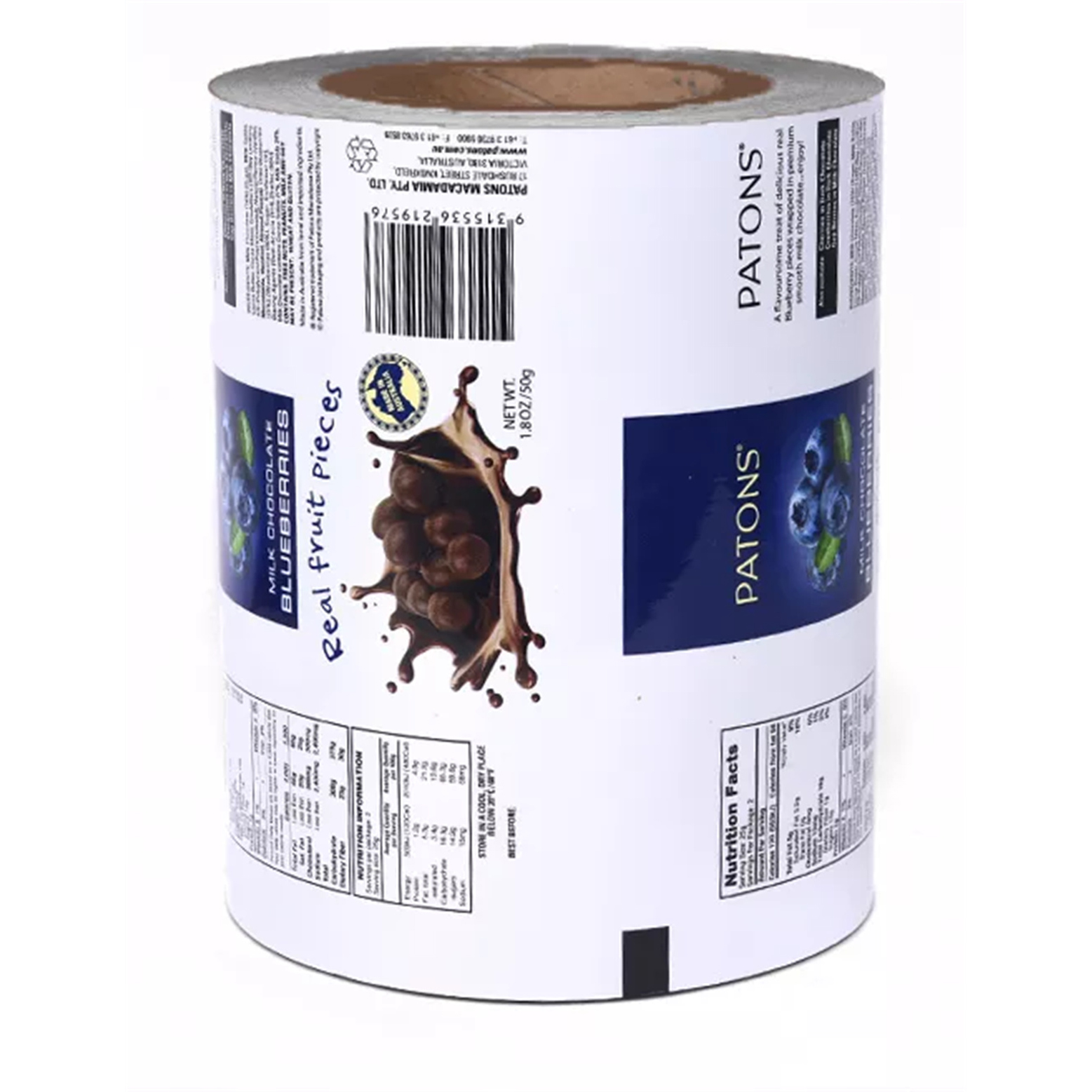
Ethylene-vinyl acetate copolymer film
EVA films, which stand out for their excellent elasticity, are often produced by extrusion blow molding. The properties of this film are closely related to the content of vinyl acetate (VA). As the VA content increases, the film improves in terms of elasticity, stress crack resistance, low temperature resistance, and heat sealability. When the VA content reaches 15%~20%, its performance is even comparable to that of flexible PVC film. Conversely, when the VA content is lower, the film performance is closer to that of LDPE film. Generally, the content of VA in EVA film is controlled in the range of 10%~20%.
EVA films are known for their transparency, softness, and self-adhesiveness to the comfortable feel. Its excellent stress crack resistance and high elasticity make the elongation as high as 59%~80%, making it an ideal spiral wound film. In the field of packaging, it is widely used in the collection and wrapping of boxes and bagged goods, as well as the stretch wrapping of pallets. At the same time, EVA film is also suitable for the production of packaging bags for heavy materials such as fertilizers and chemical raw materials. In addition, it has excellent low-temperature heat sealing and inclusion sealing, and is often used as a heat sealing layer for composite films.
Polyvinyl alcohol film
The production methods of PVA films include solution casting and extrusion blow molding. Due to the high melting temperature of PVA and its proximity to the decomposition temperature, direct melt extrusion is difficult, so water plasticization is often used to reduce the processing temperature. In this way, the film needs to be dried and dehydrated after molding to obtain a practical PVA film. In the field of packaging, the industry prefers to use the cast method to produce PVA films.
PVA films can be divided into water-resistant films and water-soluble films. Water-resistant films are made of PVA with a polymerization degree of more than 1000 and completely saponified, while water-soluble films are made of partially saponified PVA with a low degree of polymerization. In packaging applications, we mainly use water-resistant PVA films.
PVA film, which stands out for its excellent transparency and gloss, is not only less prone to static electricity accumulation and dust absorption, but also has good printing performance. In the dry state, it exhibits excellent airtightness and fragrance retention, as well as excellent oil resistance. In addition, PVA films have good mechanical strength, toughness, and resistance to stress cracking, and can be heat-sealed. However, due to its high moisture permeability and strong water absorption, the dimensional stability needs to be improved. In order to solve this problem, polyvinylidene chloride coating, i.e., K coating, is usually used to enhance its air tightness, fragrance retention and moisture resistance. This specially treated PVA film is ideal for food packaging.
PVA film is often used as a barrier layer for composite films, and is widely used in the packaging of fast food, meat products, cream products and other foods. At the same time, its single film is also widely used in the packaging of textiles and clothing. In addition, water-soluble PVA films also have excellent performance in the metering and packaging of chemical products such as disinfectants, detergents, bleach, dyes, pesticides, etc., as well as the washing bags of patients' clothes.
In general, plastic packaging films are indispensable in the field of packaging, and their unique properties enable them to meet a variety of complex and demanding packaging needs.
Post time: Mar-18-2025